Welding WPS: Usual Blunders to Prevent and Exactly How to Correct Them
Mastering Welding WPS Standards: Ideal Practices and Techniques for High Quality Welds
In the realm of welding, understanding Welding Treatment Specification (WPS) requirements is a critical component that directly influences the high quality and honesty of welds. As we browse with the details of welding WPS requirements, revealing essential understandings and techniques for achieving top-tier welds will certainly be vital for welders seeking to excel in their craft and generate welds that stand the test of time.
Comprehending Welding WPS Standards

Assessors rely on WPS paperwork to confirm that welding treatments are being complied with appropriately and that the resulting welds are of high quality. Designers utilize WPS standards to create welding procedures that make sure the durability and dependability of welded frameworks.
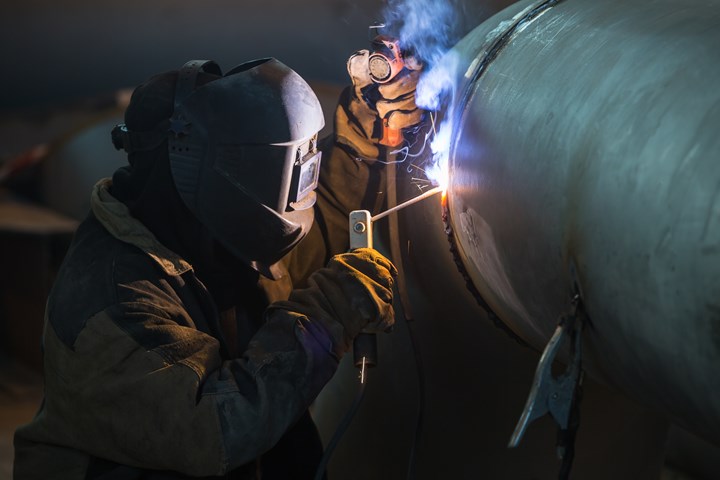

Essential Tools for Quality Welds
Understanding welding WPS requirements is crucial for welders to properly utilize the important devices required for creating top quality welds. The type of welding maker needed depends on the welding process being used, such as MIG, TIG, or stick welding. Cable brushes and chipping hammers are essential for cleaning up the weld joint prior to and after welding to get rid of any impurities that can affect the quality of the weld.
Key Methods for Welding Success
To attain welding success, one must understand the key techniques crucial for generating premium welds. Keeping a consistent hand and a stable welding placement throughout the process is crucial to attaining precision and uniformity in the welds. By understanding these vital strategies, welders can raise the quality of their work and attain welding success.
Ensuring Compliance With WPS Requirements
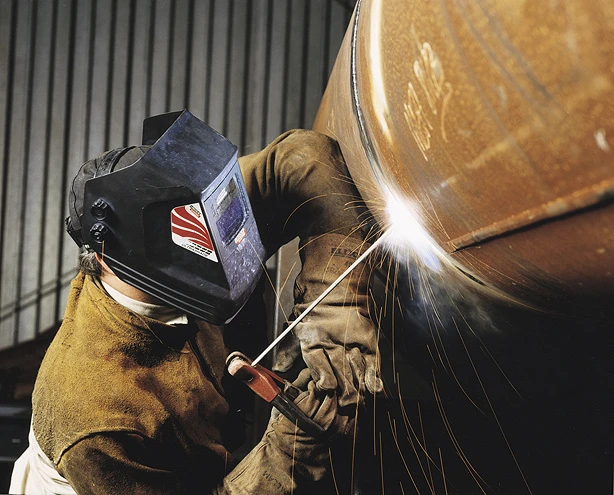
Additionally, welders need to undergo training to acquaint themselves with the WPS requirements relevant to their job. Regular audits and assessments should be performed to validate that welding activities line up with the suggested WPS standards. Additionally, preserving in-depth documents of welding criteria, tools calibration, and examination results is crucial for demonstrating compliance with WPS standards - welding WPS. By carefully adhering to WPS criteria, welders can make sure that their work meets the needed high quality levels and contributes to the total success of the welding job.
Troubleshooting Common Welding Issues
When confronted with usual welding issues, identifying the source is critical for reliable troubleshooting. One common trouble is the existence of porosity in welds, see this frequently caused by contaminants such as oil, corrosion, or moisture. To resolve this, making certain proper cleaning of the base metal prior to welding and utilizing the proper securing gas can significantly decrease porosity. One more concern often encountered is lack of blend, where the weld fails to properly bond with the base product. This can stem from insufficient heat input or inappropriate welding method. Adjusting parameters such as voltage, wire feed speed, or travel rate can assist enhance blend. Furthermore, distortion, fracturing, and spatter are typical site here welding obstacles that can be minimized with appropriate joint preparation, regular heat control, and selecting the suitable welding consumables. By thoroughly understanding these common welding issues and their origin, welders can efficiently troubleshoot troubles and attain top quality welds.
Conclusion
In final thought, grasping welding WPS criteria requires an extensive understanding of the standards, utilizing essential tools, and carrying out vital methods for effective welds. Ensuring conformity with WPS standards is critical for creating quality welds and staying clear of typical welding problems. By complying with best methods and practices, welders can accomplish dependable and consistent outcomes in their welding projects.
In the world of welding, grasping Welding Procedure Requirements (WPS) requirements is a critical part that straight affects the quality and honesty of welds.When diving right into the realm of websites welding methods, an essential facet to comprehend is the value and details of Welding Procedure Requirements (WPS) criteria. WPS standards provide an in-depth guideline for welding operations, guaranteeing uniformity, high quality, and security in the welding process. The kind of welding device required depends on the welding process being used, such as MIG, TIG, or stick welding.Achieving welding success with the mastery of essential strategies requires a detailed understanding and adherence to Welding Procedure Spec (WPS) standards.